Reliability in the broad sense is the science aimed at predicting, analyzing, preventing and mitigating failures over time.
Reliability in the narrow sense is the probability that a device will operate successfully for a specific period of time and under specified conditions when used in the manner and for the purpose intended.
You cannot purchase the reliability separately and add to your product for decreasing your expenses in the field (warranty period).
The reliability assurance or improvement is an integrative process during development, production and field operation phases that must be implemented according to the internal standards for each designed product.
You should make appropriate investment during design and production for developing a reliable product that will result in saving more money during product warranty period.
Your warranty policy should be based on product reliability analysis.
Why is it important?
Who Gains From Good Reliability?
Reliability-related costs
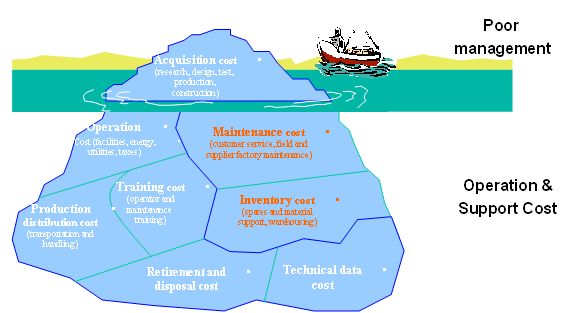
• Your company's culture must incorporate proper understanding of reliability importance. This may require painful compromises in some areas.
• Quantitative assessments of Product Reliability must focus on identification and timely elimination of Design and Processing deficiencies that degrade product performance and operating life expectancy.
• Communication channels with your customers must be open and formalized to capture their detailed comments related to product failures.
• A well-conceived failure database of product field failure modes supported by analysis of their root causes is fundamental to corrective action and improvement.
• Reliability must be designed into products and be included in all aspects of business. The design and development engineering team should take the primary responsibility of your company's product reliability. Formal product development processes and good project management practices are required.
• Your procurement group must drive supplier quality and reliability through partnering.
• Manufacturing has to use modern quality control methods to ensure that components and the whole systems are produced according to specification with negligible variation.
Reliability Analysis
Reliability Prediction
Reliability Services by ALD
Reliability Prediction Software
Reliability Analysis Software