Maintainability Prediction and Analysis in RAM Commander is based on the MIL-HDBK-472, 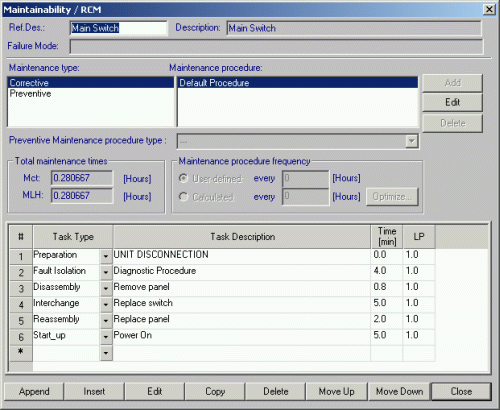
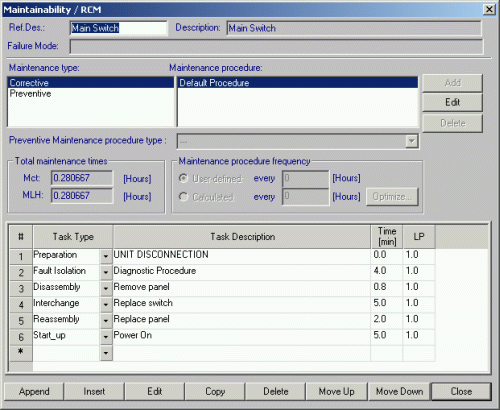
Procedure V, Method A. Maintainability module is used to predict maintainability of systems and equipment of any type,
including avionics, ground and shipboard electronics, mechanical equipment, etc., at all levels of maintenance.
Maintainability Module Features
• 5 customizable levels of Repair and Replace for tree elements
• Corrective Maintenance procedure per element or Failure Mode
• Preventive Maintenance procedures per element or Failure Mode
• Preventive Maintenance procedure frequency optimization
• Standard Times and Standard Tasks libraries
• List of required skills, equipment and materials for each task
• Skills, Equipment and Materials Libraries
• RCM (Reliability-Centered Maintenance)
• A wide range of reports for Maintainability Analysis
• Required skills, materials and equipment calculation
Primary Results provided by Maintainability Module
•Mean Time To Repair (MTTR)
•Maintenance Corrective Time (Mct)
•Ambiguity factor - the average number of iterations required to correct a fault (can be automatically calculated from the Testability Analysis).
•Maximum Corrective Maintenance Time for the f-th percentile (Mctmax(f))
•Mean Maintenance Man-hours per repair (MMH/repair)
•Mean Man-hours per Operating Hour (MMH/OH)
Primary Reports Generated by Maintainability Module
•Maintenance Tasks Analysis (MTA) report provides a prediction of work load for each skill type and equipment, and material usage:
MTA: Information | Item. Maintenance Task, required skills, equipment and materials for each task |
MTA: Skills summary | Calculation of Total Labour Hours per year for each skill type, according to system usage scenario |
MTA: STE summary | Calculation of Total Labour Hours per year for each equipment type, according to system usage scenario |
MTA: Material summary | Calculation of material consumption for maintenance tasks per year for each material, according to system usage scenario |
•Maintenance Engineering Analysis (MEA) — displaying the time period for each maintenance task and is used in Integrated Logistics Support
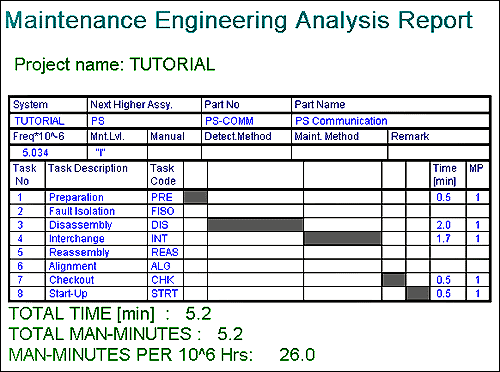
RCM (Reliability Centered Maintenance) Module
RCM utilizes a systematic engineering approach to determine a complete set of maintenance tasks in order to minimize failures and maximize reliability. RCM also provides the foundation for understanding why certain maintenance tasks are performed and the justification for eliminating unnecessary Preventive Maintenance (PM) activities. It is the optimal mix between the Corrective, Preventive, and Condition-Based maintenance. RCM is a function-oriented approach which considers mission importance, environment, safety, security, economics and regulation requirements.
The RCM analysis process consists of 7 main steps/questions. Each step is supported by the RCM module of RAM Commander:
1. System definition (Product Tree and/or Functional blocks)
2. Significant Functions Identification
3. Functional Failures determination
4. FMECA analysis, Failure Consequence Categorization
5. Most Appropriate Maintenance Policy and Failure Management Strategy Selection
6. Preventive Maintenance Tasks and Frequency Optimization
7. Failure Management Policy - Corrective Maintenance and Run-to-Failure
See also:
RAM Commander homepage
ALD Reliability and Safety Software Overview
Reliability&Safety Software Download
See ALD Reliability, Safety and Quality Services if you wish us to perform reliability prediction, analysis or other activities for you