FMEA stands for Failure Mode and Effects Analysis.
There are two major approaches to FMEA analysis with the similar names, and ALD has two separate software tools for each of these types: Potential FMEA and hardware/functional FMECA
1. Potential Failure Mode and Effects Analysis (FMEA) is widely used by manufacturing industries during various phases of the product life cycle. Recently the service industries have started applying this methodology more extensively. Potential FMEA is described by AIAG, QS-9000, SAE J 1739, IEC 60812, JEP131 and other standards, sometimes is called "automotive" or "AIAG" (Automotive Industry Action Group) FMEA. It is required by many other standards like ISO 14971 (Application of risk management to medical devices) and more.
Potential FMEA is an analytical technique utilized to assure that as a mean to assure that potential failure modes and their associated causes/mechanisms have been considered and addressed to the extent possible. Corrective actions are suggested and selected for implementation, and a control plan is formed as a part of the procedure.
Potential FMEA deals with Severity, Occurrence and Detection rankings. Multiplication of these three ranks gives us a Risk Priority Number (RPN), which is an integrated measure of risk.
Any entity like product, process, software, or system may be a subject of this analysis.
The screenshot below illustrates FMEA example done using RAM Commander software:
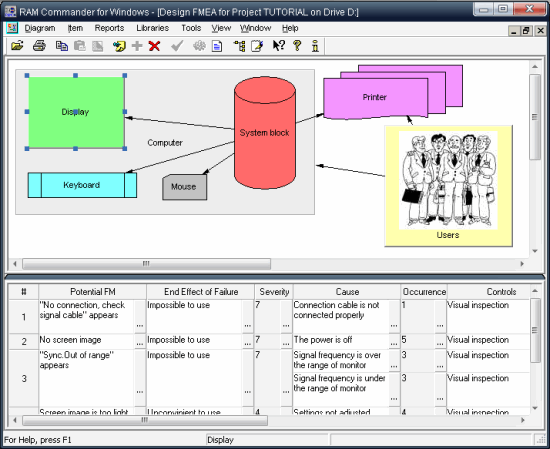
See RAM Commander Potential FMEA Software Module for more information about this FMEA type.
2. Hardware FMEA and FMECA (Failure Mode, Effects and Criticality Analysis) is one of the major components of system reliability analysis. It is required and compatible with MIL-STD-1629A and other standards (like GJB 1391, GJB 1392, AIR FORCE SMC REGULATION 800-31 and more). Many standards and regulations for aerospace, defense, telecommunications, electronics and other industries require that FMECA analysis must be performed for all designed/manufactured/acquisition systems, especially if they are mission or safety critical.
FMECA includes failure analysis, criticality analysis and testability analysis. FMECA is designed to analyze different failure modes and their effects on the system, classify and prioritize end effects level of importance based on failure rate and severity of the failure effect.
Testability analysis is also a part of FMECA module and is used to analyze methods of failure mode detection/isolation, perform fault diagnostics, validate test efficiency and find undetectable failures.
FMECA module uses a product tree previously created for the reliability analysis purposes. It also incorporates reliability and maintainability information received as a result of reliability and maintainability analysis.
The screenshot below illustrates FMECA example provided by the RAM Commander software:
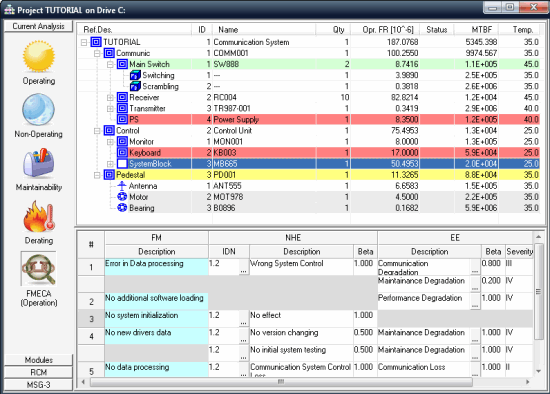
See RAM Commander FMECA and Testability Software Module for more information about this FMEA type.
See also:
RAM Commander homepage
ALD Reliability and Safety Software Overview
See ALD Reliability, Safety and Quality Services if you wish us to perform reliability prediction, analysis or other activities for you
FMECA module uses a product tree previously created for the reliability analysis purposes. It also incorporates reliability and maintainability information received as a result of reliability and maintainability analysis.
The screenshot below illustrates FMECA example provided by the RAM Commander software:
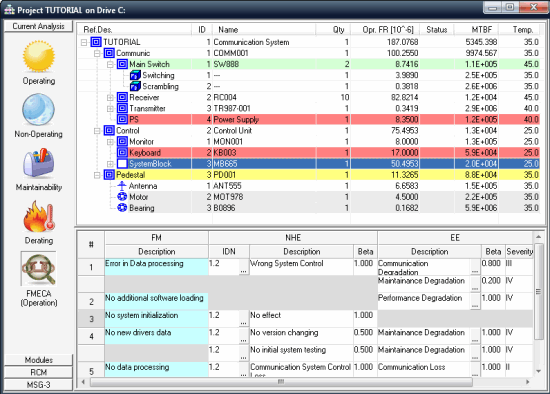
See RAM Commander FMECA and Testability Software Module for more information about this FMEA type.
See also:
RAM Commander homepage
ALD Reliability and Safety Software Overview
See ALD Reliability, Safety and Quality Services if you wish us to perform reliability prediction, analysis or other activities for you